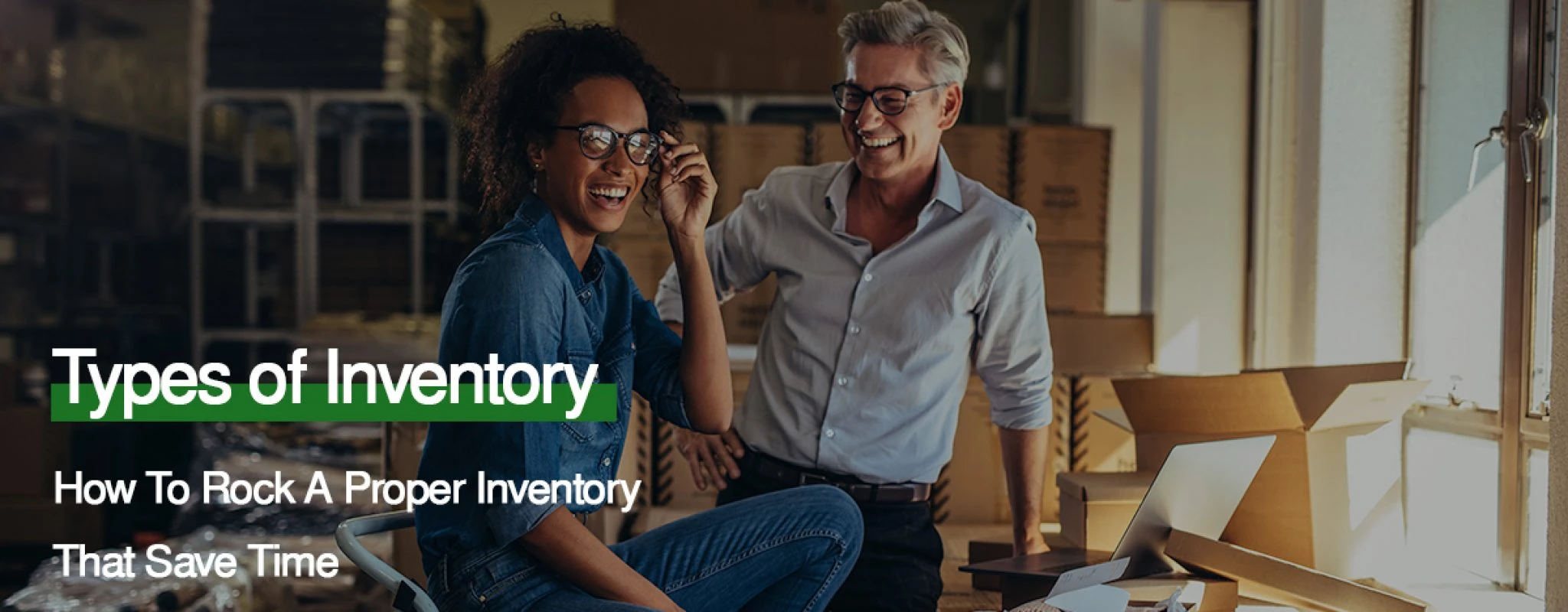
November 25th, 2020
How To Rock A Proper Inventory That Save Time
You are viewing an article about Ricemill Classic. Check out our new shipping app for Australia sellers.
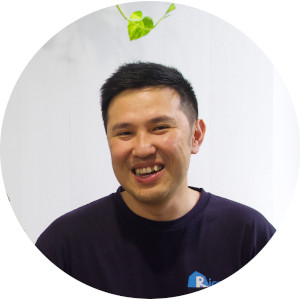
Chew Lim
There is no fixed or certain way to handle or control inventory stocks. Knowing what type of inventory there are can go a long way in teaching you how to manage them, distinguishing a successful company from a failing one. That is what makes understanding inventory types critical to companies. It helps you figure out the most efficient ways for inventory management.
We at Ricemill hope that you learn the different types of inventory and figure out which method is best suited to your business with this article. No doubt inventory management is a key issue in your business. That is why you should first understand what inventory management is before you go ahead to learning how to manage your inventory.
What is inventory management?
Inventory management is the process of ordering, handling, storing, and using a company’s non-capitalised assets – AKA its inventory. For some businesses, this involves raw materials and components, while others may only deal with finished stock items ready for sale.
Either way, inventory management all comes down to balance – having the right amount of stock, in the right place, at the right time. And this guide will help you achieve just that.
Retail inventory management
If you’re a retail company, your inventory (products) and customers are different from the inventory and customers production companies have. Because of this unique difference, special attention is paid to the nature of your inventory. Retail is the general term used to describe businesses that sell physical products to consumers. While not exclusive to retail, inventory management tends to play more of a role in this industry than any other.
We’ll therefore be focusing mainly on inventory management from a retail perspective within this guide.
Retail can be split into several areas:
-
Offline. Where a company sells via a brick-and-mortar store or physical location.
-
Online. Where a company sells over the internet via an ecommerce website or marketplace.
-
Multichannel. Where a company sells in multiple different places, usually a combination of online websites and marketplaces.
-
Omnichannel. Where a company provides a unified, integrated experience for customers across all the different online and offline channels it sells on.
Businesses may also choose to trade via wholesale channels. This involves selling inventory (usually in bulk) directly business-to-business (B2B) or taking part in B2B ecommerce.
A company’s inventory will therefore need to be managed in accordance with which of these retail models it operates within.
What are the types of inventory?
There are five fundamental types of inventory that cover the different types of products your company might sell. They are
-
Raw materials
-
Work in progress (WIP) inventory
-
Finished goods (we can also break finished goods into subcategories, which we will be discussing further on in this article).
-
Maintenance, repair, and operations (MRO) goods.
-
Packing materials
Let us explore each of these inventory types further.
- Raw materials
Raw materials are considered any item(s) used in the process of creating finished products. These raw materials can be produced or stored by the business itself, and they can be purchased from a supplier.
For example:
Imagine a business that makes its office furniture, but they produce the wood firm a supplier. On the other hand, there is a company that supplies coffee beans, and unlike the first company, they grow these beans on their own.
In both cases, the raw materials they consume are still considered a type of inventory. They must be adequately managed, stored, and accounted for.
- Work in progress (WIP) inventory
Work in progress or WIP inventory refers to retailers that manufacture their products. These inventory categories are still unfinished items or components currently in production and are not yet ready to be put for sale.
Like in the coffee business example, this may be the coffee seeds just after harvest before dried or roasted.
- Finished goods
Finished goods are probably the most valuable type of inventory. This is because they have undergone every process of production, and they are ready for sale. The business itself may have manufactured these products or purchased as a whole as finished products from a supplier.
This type of inventory is mostly found in retailers’ stores, and they will either purchase finished products from a supplier or request that manufacturers produce custom products on their behalf.
Because of this, finished goods are often but not always the type of inventory that needs to be managed properly. However, retail managers who are wise enough to use inventory management software do not encounter this challenge. Our inventory management software helps manage your inventory better thanks to several of its critical features discussed below. This helps multi channel sellers across australia have better control of their inventory.
- Maintenance, repair, and operations (MRO) goods
Maintenance, repair, and operations are also known as MRO goods used within the manufacture of products. Still, they do not make up any part of the finished product.
Here are some of the items that fall into this category:
-
Production and repair tools
-
Uniforms and safety equipment
-
Cleaning supplies
-
Machinery
-
Batteries
-
Computer systems.
Take a careful look at each item. You will realize that each of these items is consumed or discarded in manufacturing finished goods. Still, you do not see them directly on the finished goods.
This type of inventory is usually menial and small in quantity. Nevertheless, MRO still needs to be purchased from a supplier. They will need to be stored somewhere and accounted for in your financial records.
- Packing materials
Inventory that falls under this category is anything you use in packing and protecting goods either while they are in storage or transit to customers. This makes this type of inventory very common for eCommerce stores. They usually include things like:
- Bubble wraps.
- Padding
- Packing chips
- Packing boxes
When managing inventory, many retailers ignore packing materials as an important item to consider. However, the stock of these items needs to be used and maintained regularly, which, in reality, makes them very important and worthy of being mentioned in the comprehensive inventory report and account.
The different categories of finished goods
Earlier on, we mentioned that there are subcategories to the finished goods type of inventory. Within a retail ecommerce context, it is helpful to subdivide the finished goods into five categories. This helps a business manage its inventory better as it gives more visibility and allows for improved allocation and management.
Under the finished-good type of inventory, you can subdivide into:
Ready for sale
This is also called available inventory. It refers to stock that has been manufactured or purchased and was put away in warehouses for storage ready for sale. These are products that can be selected, packaged, and shipped without complications.
Allocated
This is the type of inventory that has been bought by a customer, and it is waiting to be delivered as it has been allocated to the sale order. That means such inventory isn’t eligible for sale anymore, and they are removed from the available inventory figure.
In transit
This is an unsold inventory that is on the move. You can consider it a purchase order in transit or inventory, which is being moved from one warehouse to another.
Seasonal
This is also known as anticipation stock. It is inventory that has been manufactured or purchased to cover a predicted upturn in demand specifically. It is common to see retailers buy more than their current demand to cover their black Friday sales or meet their peak seasons’ demand.
Safety
This type acts as a safety net to protect you in a sudden upturn in demand or encounter problems with the supply.
Ricemill inventory management software
Using a software obviously has its many benefits. By using our software, you gain better control of your inventory and you can manage it more efficiently. This will help your business grow steadily with proper documentation of inventory. By using our software you enjoy:
- Real-time tracking. Syncs a live inventory figure across all sales channels and warehouses.
- Forecasting. Uses past sales data to project estimated inventory requirements into the future.
- Purchasing. Helps manage all suppliers and purchase orders for quick and easy stock replenishment.
- Rules & automations. Allows creation of inventory rules, e.g. to dictate how much stock shows on each sales channel.
- Cloud-based. Accessed from anywhere with data never being overwritten by team members making changes.
Conclusion
You must learn these types of inventory as each one requires a different approach to management. Knowing and categorising the different types of inventory is critical to proper inventory management. As an Aussie retailer, you can employ Ricemill software to perform all your inventory audits and management with accuracy and convenience.
Are you selling on multiple sales channels? Improve your sales today by getting started with Ricemill.